Industrie 4.0 : quelle réalité en 2019 ?
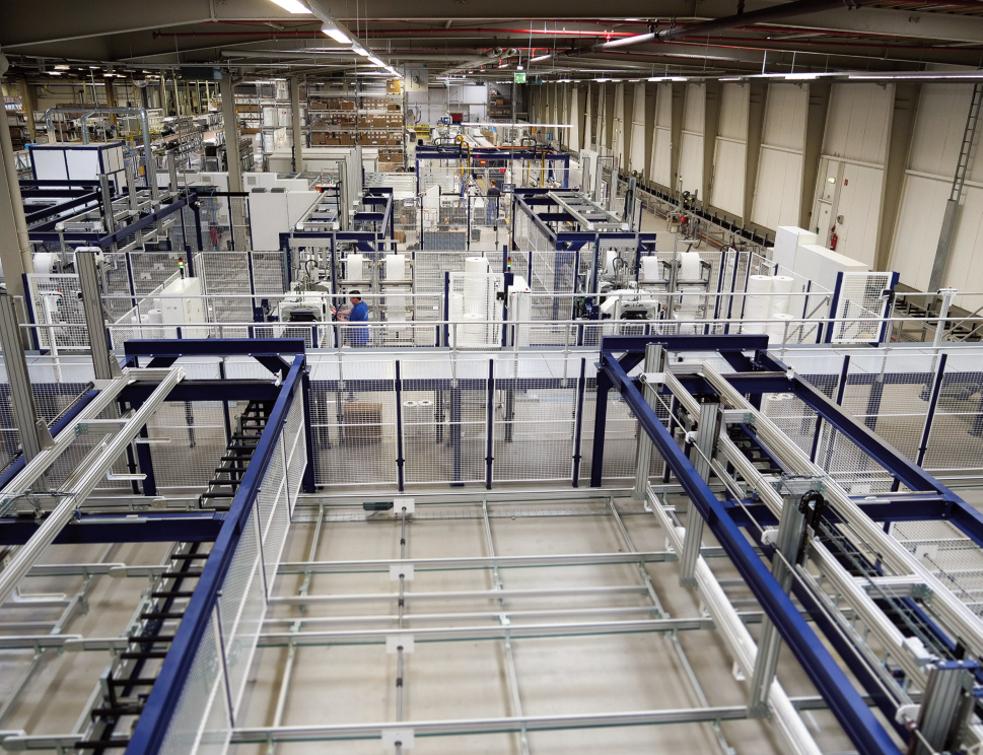
© Heroal Dans le secteur, l’usine 4.0 commence à poindre son nez. Si la révolution est en marche, les projets de construction ou de transformation d’unités de production adaptées sont encore peu nombreux…
« En Italie, nous avons été favorisé par des aides qui ont encouragé les industriels à s’équiper de machines connectées », remarque Pascal Royannais, directeur commercial verre du groupe Biesse.
© V&MA
Mais en France plusieurs types de machines – automatiques connectées ou pas, semi-automatiques voire manuelles – cohabitent encore dans les ateliers. Pour passer au 4.0, les équipements doivent être connectés à Internet. « Il faut aussi que l’entreprise ait accès au haut débit, ce qui n’est pas encore le cas partout et représente un frein », pointe Pascal Royannais.
Avec Sophia, une appli mobile permet de contrôler les performances des machines du groupe Biesse © Biesse
Les fournisseurs n’exigent même pas la fibre, mais du haut débit qui fait défaut dans certains territoires. Enfin, les acteurs du secteur doivent s’intéresser au sujet.
Atlantem construit son usine 4.0
Atlantem Industrie devrait fournir d’ici quelques mois un bel exemple d’une usine 4.0. L’entreprise investit 20 M€ (bâtiment et équipements industriels) dans la construction et l’aménagement d’un nouveau site (18 000 m²) à Saint-Sauveur-des-Landes dans la communauté de communes de Fougères (35). Le site qui devrait être mis en service en septembre 2019 prévoit d’employer jusqu’à 150 collaborateurs (dont 50 recrutements). Son objectif ? Optimiser la production tout en gérant le bien-être au travail et répondre efficacement aux besoins des clients. Des outils numériques et des méthodes d’organisation de la chaîne logistique sont conçus pour optimiser les processus. Ainsi, le site intègrera un transstockeur, des chariots autonomes AGV, etc. Dans le cadre d’une démarche RSE, un travail de fond a été effectué sur le pilotage des flux de matières internes par radioguidage, la digitalisation du flux d’informations, les économies d’énergie et de matières premières, ainsi que le recyclage des déchets. L’ergonomie des postes de travail a été totalement repensée et validée à l’aide de la réalité virtuelle (éclairage naturel, suppression des ports de charge, etc.). « Nous avons demandé à nos fournisseurs d’équipement de nous proposer des maquettes 3D afin que les opérateurs puissent travailler sur ces maquettes virtuelles, vérifier et détecter les gestes inappropriés afin de les corriger », commente Bruno Cadudal, directeur général d’Atlantem Industries.
La future usine devrait augmenter la capacité de production de la menuiserie AM-X © Atlantem Industries |
Le concept 4.0
L’industrie 4.0 désigne une nouvelle génération d’usines connectées, issue de la convergence entre les technologies de l’information et de la communication (le Web) et les technologies de production. « L’industrie 4.0 est une industrie efficace et souple, la technologie vient en support des ressources humaines, pour améliorer les processus de production, livrer le client avec une qualité meilleure, dans des délais plus courts et à des coûts maîtrisés », résume Joan Bonnafous, directeur opérations Toulouse de Technal.
Technal a robotisé 2 lignes de production de profilés à rupture de pont thermique © Technal
Le parc de machines communique aussi bien en interne qu’à l’extérieur. « Une application mobile affiche en temps réel le rendement des machines, mentionne les arrêts éventuels, le nombre de programmes menés à leur terme ; avec ces statistiques, le responsable de production peut connaître très précisément la capacité de production de chaque machine », ajoute Pascal Royannais. Revers de la médaille, il peut aussi exercer son sens critique…
Il n’empêche, « la 4e révolution industrielle est en cours, elle répond aux enjeux liés à la personnalisation des produits fabriqués dans des usines totalement repensées, afin que l’information circule mieux et soit accessible en temps réel », constate Nicolas Maritan, directeur marketing et communication d’Elcia. Car ces usines, dites intelligentes, exploitent les données.
« Aucune organisation industrielle ne devrait passer à côté de l’évolution des machines, équipées d’un cerveau, et donc capables à la fois d’intégrer des informations et d’en renvoyer, car l’industrie 4.0 ne se limite pas à la machine, mais englobe l’ERP et le retour des données sur une plateforme du fournisseur des machines ; l’intelligence est exploitée au-delà de la production », confirme Eric Mercier, responsable commercial de Bottero.
Sepalumic agrandit ses entrepôts et son usine de laquage
« En 2019, deux sites sont transformés. Le dépôt de Bourg-des-Comptes en Bretagne et Genlis, près de Dijon, sont agrandis », déclare Aurélien Briscadieu, chargé de marketing Sepalumic. Le premier bénéficie de 2 000 m² supplémentaires et doit absorber aussi bien les commandes à gros volumes que les petites. Ses clients, préfabricateurs industriels notamment, utilisent des barres 7016 et blanches qui doivent être présentes en stock – suivant une méthode de roulement juste-à-temps (Kanban) – pour répondre à leurs attentes. Le but étant de réduire les délais, y compris pour les commandes de produits plus diffus (rose, bleu, etc.). Par ailleurs, l’évolution de l’usine de laquage à Genlis (Côte d’Or), doit permettre de traiter les commandes en diffus. « Nous devons répondre aux besoins des fabricants installateurs et des industriels avec plus de références, donc plus de combinaisons de couleurs, tout en tenant des délais standards », commente Aurélien Briscadieu. Un enjeu important qui nécessite des investissements importants. L’usine de Genlis, précédemment modernisée, dispose, entre autres, d’un transstockeur.
Le dépôt Sepalumic de Bourg-des-Comptes en Bretagne © Sepalumic |
Technologies déployées
Chez Technal, Joan Bonnafous évoque « des capteurs connectés installés récemment pour comprendre pourquoi dans 2 % des cas, certaines pièces sont défectueuses et pas les autres », ou encore la robotisation des tâches. Parmi les derniers investissements réalisés, Technal s’est doté de capteurs connectés de température dédiés à ses procédés d’extrusion. La robotisation est également d’actualité, même si elle ne représente qu’un aspect du 4.0, concept beaucoup plus global. « Technal a robotisé l’alimentation des deux lignes de production de profilés à rupture de pont thermique, la robotisation permet d’augmenter les capacités de production, tout en supprimant les problèmes d’ergonomie », indique Joan Bonnafous. « Il faut du temps pour maîtriser la technologie, mais aujourd’hui nous sommes très satisfaits des résultats », se félicite-t-il.
KSM investit 5 M€
KSM a investi dans l'agrandissement de ses bâtiments (unité de laquage, de fabrication et logistique). L'extension porte sur 2 500 m² d'atelier supplémentaire, pour un total de 13 000 m².
KSM agrandit ses locaux © KSM
Un investissement global qui s'élève à 5 M€, comprenant la modernisation de la chaîne de laquage et des nouveaux investissements pour la fabrication des portails (une poinçonneuse et découpe laser, deux plieuses dernière génération, une chaîne de laquage). « Tous ces investissements ont pour objectif de répondre à la demande toujours plus précise de personnalisation du produit, tout en gardant une logique industrielle pour rationaliser les coûts », informe Sandrine Cuvilliez, responsable ADV et marketing. « Notre concept de fabrication exige plus de performances en qualité de laquage car nos portails sont entièrement soudés et montés en brut, puis laqués dans leur ensemble pour assurer une homogénéité de laque, ce qui nous différencie de l’offre de produit assemblé. Le portail soudé bénéficie en effet d’une meilleure tenue dans le temps. En parallèle, nous avons également adapté nos quais dédiés au transport, avec des quais niveleurs pour faciliter le chargement des marchandises ».
KSM améliore ses quais de chargement © KSM |
Côté logiciel, Gilles Le Bagousse, directeur commercial de FOM Industrie précise que « les lignes automatisées dépendent à 100 % des logiciels qui les guident, soit via des solutions comme Chacal ou Orgadata, soit via des solutions "maison" développées par les gammistes ; nous sommes partenaires des uns et des autres ». L’ERP est la clé de voûte du système. « Nous accompagnons nos clients avec Diapason, colonne vertébrale pour centraliser l’information et la restituer ; nous travaillons par exemple d’un côté, à l’intégration de l’outil de vente afin de donner de la visibilité au consommateur final, de l’autre, la centralisation des commandes permet de faire des recommandations de lots à la production », explique Nicolas Maritan.
Montée en compétences et sécurité
Quels sont les apports pour les ressources humaines ? Multiples, à priori. D’abord, l’industrie 4.0 permet de faire monter les opérateurs en compétences. Avec la robotisation des tâches, les métiers se transforment. « Les opérateurs sont plus qualifiés, ils supervisent au lieu d’exécuter des tâches répétitives », observe Nicolas Maritan. Une transformation que Technal a vécue lors de la robotisation de lignes de production. « Les postes de travail mécaniques étant supprimés, nous avons créé des postes de superviseurs et nous avons vu des collaborateurs se révéler », se réjouit Joan Bonnafous. Gilles Le Bagousse, complète : « les profils viennent davantage de BTS de productique et de maintenance ».
Depuis deux ans, FenêtréA accompagne sa transformation d’un projet de Lean facturing. « Nous sommes à l’écoute des besoins des opérateurs, le 4.0 passe par les collaborateurs, le management évolue, il est inclus dans la démarche », souligne Jean-Baptiste Gevresse, directeur industriel de FenêtréA.
Interface de configuration gamme Open © FenêtréA
D’ailleurs, comme l’affirme Sébastien Joly, directeur marketing et communication de Riou Glass, « l’automatisation permet, en supprimant les manipulations, de renforcer la sécurité au travail et donc de préserver la santé de l’opérateur ». Riou Glass s’intéresse de près aux innovations. « Nous avons testé un exosquelette qui porte des verres de 100 kg comme un livre, nous ne sommes pas encore équipés, mais minimiser les manipulations fait partie de nos enjeux », déclare Sébastien Joly. Un gant connecté pour piloter les ponts roulants est également à l’étude…
Chez FPEE, qui a investi près de 8 M€ dans la modernisation de son usine aluminium, et installé un transstockeur, l’objectif est clairement « d’améliorer les conditions de travail des salariés, en évitant les ports de charge importants, avec bien sûr un impact positif sur la qualité de la production, puisqu’il n’y a plus de manipulation, et sur la productivité », assure Cécile Sanz, présidente du groupe. L’implantation de l’outil a pu être réalisé grâce à un agrandissement du bâtiment. « Nous avons axé nos investissements sur l’amélioration des conditions de travail plus que sur la productivité, car pour atteindre un niveau de productivité plus important, il faudrait perdre en agilité, or compte tenu de notre largeur
de gamme, nous avons besoin d’un outil industriel agile », confie la dirigeante. L’automatisation de la production s’est donc opérée dans la limite du niveau d’agilité souhaité.
L’amélioration des conditions de travail, une priorité pour FPEE ! © FPEE
Le Cetim en mode recherche…
Cetim, centre d’expertise mécanique français, s’associe avec des laboratoires spécialisés dans la recherche fondamentale afin de contribuer aux progrès techniques des entreprises mécaniciennes. Ainsi, le Laboratoire d’usinage et de procédés de mise en oeuvre des poudres en fabrication additive (Luppiam) cherche à faire progresser les technologies majeures pour les industriels avec la mise en synergie des moyens et des compétences de l’institut Carnot Cetim, de l’École nationale d’ingénieurs de Saint-Étienne (Énise) et de l’École des Mines de Saint-Étienne (EMSE) au sein d’un laboratoire commun.
Actuellement, trois thèses en usinage sont conduites au sein du laboratoire. Une première vise à réduire l’usure des outils coupants via une nouvelle approche de simulation, validée sur des cas industriels. Deux autres se concentrent sur la prédiction des contraintes résiduelles induites en tournage et en perçage. Dans le même domaine, le projet FUI "Impulsa" consiste à anticiper par la modélisation, les déformations mécaniques et thermiques des pièces dès leur programmation sur machines-outils.
Philippe Choderlos de Laclos, directeur général du Cetim © Cetim
Philippe Choderlos de Laclos, directeur général du Cetim s’est félicité, à l’occasion de la publication du rapport de l’Académie des Technologies fin septembre 2018, de la montée en compétences technologiques des PME et de voir le Centre technique industriel reconnu comme acteur national de la transformation des PME et ETI industrielles. L’objectif est ambitieux : sensibiliser 30 000 PME industrielles (c’est-à-dire la quasi-totalité du tissu national) au numérique d’ici 2022. Une belle feuille de route pour l’Alliance Industrie du Futur. |
Dans les entreprises, le projet 4.0, comme tout changement organisationnel, doit être accompagné. Chez Technal, les équipes ont travaillé très en amont sur la robotisation, la partie la plus impactante au plan social et en termes d’organisation du travail. « Nous avons associé les équipes de production à la démarche afin de les familiariser avec la prise en main des robots », témoigne Joan Bonnafous.
La dimension 4.0 de Lattuada
Depuis plus de 5 ans, le fabricant italien Adelio Lattuada, notamment reconnu pour ses rectilignes et au rayonnement international, consacre des ressources internes et de considérables investissements pour la conception et réalisation de solutions intégrant les robots et l’automatisation dans une industrie 4.0 pour le marché du verre.
Michela Lattuada, responsable de la communication externe et interne d’Adelio Lattuada © V&MA
La "smart ingénierie" de Lattuada déploie un large spectre d’innovations : robot, automatisation, intégration, industrie 4.0… « alors que débute une nouvelle ère dans l’ histoire industrielle du verre, nos clients les plus avant-gardistes, voulant profiter de solutions et de technologies avancées, peuvent compter sur un très net avantage compétitif et atteindre de nouveaux résultats en termes de productivité et de flexibilité, notamment avec PLM IOT i-Like Machines (en partenariat avec Holonix) pour collecter les données de la machine en tous points du globe et Cyberal, pour une production industrielle véritablement intégrée », précise Michela Lattuada, responsable de la communication externe et interne d’Adelio Lattuada et note, « plus que les robots, c’est avant tout l’importance de l’intelligence artificielle implantée dans nos robots qui prédomine ! Nous travaillons pour rendre nos machines encore plus automatisées et intelligentes en installant des dispositifs et des capteurs de dernière génération. Grâce à un puissant logiciel de simulation, nous pouvons saisir les données et les valeurs d’une production type par exemple, et les comparer aux résultats d’un emploi hypothétique des robots permettant d’évaluer la meilleure décision pour augmenter l’efficience de la productivité ». Toujours plus ciblée, l’intégration versus Lattuada, à travers des logiciels spécifiques, élimine les opérations répétitives manuelles et unifie les opérations de contrôle en créant un système de dialogue entre des machines capables d’adopter des décisions autonomes pour maintenir des niveaux élevés de production et de sécurité en éliminant les erreurs. Depuis 40 ans, le patrimoine de connaissances et de compétences unique développé par Adelio Lattuada, a toujours su anticiper les mutations de ses métiers tout en restant avant tout au service de ses clients partenaires.
Cyberal, le nouveau minisite dédié à l’industrie 4.0 : http://cyberal.adeliolattuada.com/ © Adelio Lattuada |
Amélioration de l'expérience client
« Avant d’équiper l’usine, nous devons digitaliser la prise de commande, en amont donc, afin que le client puisse saisir sa commande et que l’ensemble du process soit automatisé jusqu’à la production », estime Jean-Bapt iste Gevresse, (FenêtréA). À l’ère de la personnalisation des produits, les consommateurs souhaitent configurer eux-mêmes leurs menuiseries, comme les automobilistes le font sur les sites Web des constructeurs. Partant de ce constat, FenêtréA
a revu son offre et lancé la gamme de portes Open, avec ouvrant interchangeable, permettant aux clients de jouer avec les couleurs ! « C’est à l’outil industriel de s’adapter à la demande », note Jean- Baptiste Gevresse, « la 4e révolution industrielle doit permettre de gagner en souplesse, en produisant un produit unique à coût maîtrisé, pour optimiser la marge et la rentabilité ». L’étape industrielle se déroule donc lors d’une seconde phase, au cours de laquelle l’usine se transforme pour devenir plus réactive. Les lignes de production, très structurées, intègrent une dose de flexibilité et sont décloisonnées.
Bouvet a également entamé depuis dix-huit mois un gros travail de digitalisation du parcours clients, pas seulement côté production, mais bien en amont. « Aujourd’hui, les clients désirent être autonomes, ce qui suppose une nouvelle organisation pour nous », commente Laurent Ternon, responsable marketing. « Dès le 6 mai, nos clients pourront réaliser leurs devis et passer leurs commandes en ligne, déclenchant ainsi le process de production », annonce Laurent Ternon. Soucieux de son indépendance, l’industriel a ainsi développé un logiciel en interne. Aucune ressaisie ne sera nécessaire. Le suivi de l’avancement de la commande pourra être consulté au fur et à mesure du process. En cas de problème, l’atelier renseigne l’ERP qui communique avec le portail. « Le client n’a plus besoin de venir chercher l’information, elle est poussée vers lui », ajoute Laurent Ternon. Dans les ateliers, listings et papiers sont supprimés, remplacés par des écrans qui équipent les postes de travail et leur divulguent les informations utiles.
© A+W
« Derrière la terminologie de plus en plus citée de l’industrie 4.0 se cachent de nouvelles possibilités contribuant à une véritable métamorphose de la production », relève Michael Küttner, responsable marketing et communication corporate senior d’A+W. « Nous expérimentons un aspect de l'industrie 4.0 encore trop souvent sous-évalué, car une "Smart Factory" ne porte pas uniquement sur la production intelligente, mais également sur une communication optimisée entre
A.B. |
Anticiper la maintenance
« L’analyse des données permet d’anticiper les pannes et donc d’optimiser les process », argumente Nicolas Maritan. Mise au point par le service R&D du groupe Biesse, la plateforme Sophia facilite le contrôle et la maintenance de la dernière génération de machines. Equipées de capteurs, celles-ci communiquent avec le système qui les identifie et les géolocalise. Le technicien Biesse peut donc alerter l’opérateur en cas de dysfonctionnement. Surtout, une base de données centralise toutes les informations relayées par les machines dans le monde. Ainsi, au moindre pépin, le technicien a accès à des suggestions de résolution de problème, inspirées des traitements antérieurs d’incidents similaires. « Lorsqu’une machine installée dans une entreprise en Ile-de-France présente un défaut électrique, le technicien basé en région lyonnaise le visualise en temps réel. La réactivité est maximale. Avant que les machines soient connectées, le temps de recherche pour identifier un problème était estimé entre 45 et 60 minutes, avec les machines connectées il est réduit à moins de 5 minutes », avance Pascal Royannais.
Un projet industriel 4.0
(De gauche à droite) Konrad Kaiser, directeur heroal et Roland Pfeiffer, directeur commercial heroal France, Luxembourg, Belgique © V&MA
A la pointe des avancées technologiques, le fabricant allemand Heroal mène un développement international depuis ses usines implantées à deux heures de Düsseldorf, avec des solutions et systèmes aluminium distribués auprès de plus |
Les premières installations étant récentes, le groupe Biesse ne dispose pas encore de retour d’expérience. « Il faut attendre six mois pour que les clients équipés maîtrisent l’ensemble des fonctionnalités », mentionne-t-il.
La prochaine étape devrait voir l’intelligence artificielle s’inviter dans les ateliers. Des capteurs fournissant l’état des pièces et leur taux d’usure…
Bottero équipe ses dernières générations de machines (la machitable de découpe du verre feuilleté 548 par exemple) de connexions 4.0 qui les relient à une plateforme d’informations. « Chaque client peut se connecter et partager ses informations. La maintenance est optimisée grâce à la technologie, l’auto diagnostic facilité et les temps d’intervention réduit », récapitule Eric Mercier.
Bystronic glass et Hegla : deux partenaires 4.0
Plus de 50 ans d'expérience pour Bystronic glass dans le développement de solutions de traitement du verre innovantes pour les industries du verre architectural Peter Nischwitz, directeur de la communication corporate Bystronic glass © V&MA
Liant étroitement machines, données, processus et applications, l’acteur majeur dans le monde du verre Bystronic glass, connecte tous ces modules de la chaîne de processus au moyen d'une gestion de données intégrée, offrant ainsi à
Daniel Kolopp, directeur d’Hegla France © V&MA
Interfaces spécifiques de commandes intuitives pour l’industrie 4.0, numérisation et interconnexion, Hegla intègre sa vision d’avenir sous la devise "Construire demain et donner un nouvel élan au présent". « Hegla améliore toujours plus la communication entre l’homme et la machine pour simplifier les tâches et réagir instantanément aux informations », développe Daniel Kolopp, directeur d’Hegla France. Maintenance, processus d’utilisation ou encore données relatives à la production, la technologie de pointe d’Hegla équipe l’industrie du verre avec des installations interconnectées autonomes, comme la nouvelle génération de logistique d’atelier avec véhicules à guidage automatique (AGV). Au centre du concept de la Smart Factory, cette solution de transport s’adapte aux ordres du système lui-même ou de l’opérateur et aux priorités des lignes d’assemblage, par exemple, entre les lignes de découpe et les postes d’usinage et les postes-tampons suivants.
A.B. |