Stockage : le maillon fort de la ligne de production
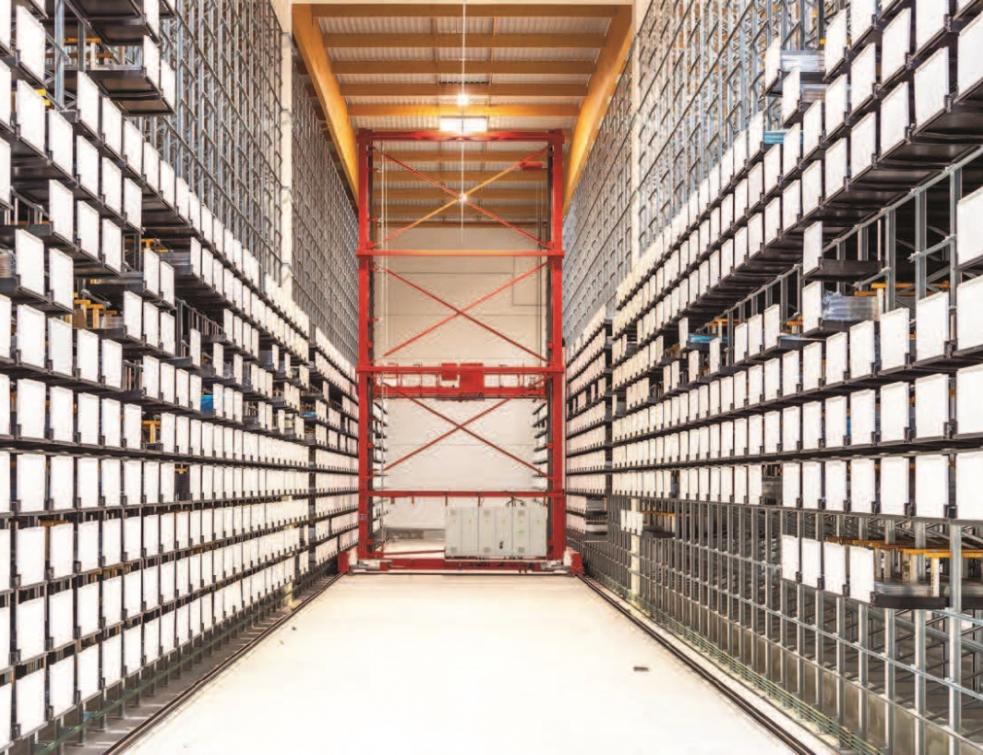
L’optimisation des flux dépend en grande partie de la capacité à bien gérer les stocks de matières premières.
« C’est un basique de toute activité humaine : organiser l’espace pour mieux l’optimiser »
Un principe qui prévaut également dans la production industrielle. Et le secteur de la menuiserie, souvent vu à la traîne par rapport à celui de l’automobile ou de l’agro-alimentaire est en passe de combler son retard. Pour y parvenir, les fabricants de solutions de stockage redoublent d’inventivité pour toujours mieux s’adapter à la réalité du terrain. C’est le cas de Tecauma, une entreprise spécialisée dans la conception, la fabrication, l’assemblage et la mise en route de machines spéciales, en particulier des solutions de manutention et de stockage automatisées et robotisées. La société basée aux Essarts en Vendée est un des leaders du secteur de la menuiserie industrielle.
© Tellier-Brise-Soleil
Toujours plus haut : Tecauma a installé un transstockeur de 14 m de haut dans le nouveau
bâtiment de Tellier-Brise-Soleil à Chemillé-en-Anjou (49) ; un atout majeur pour l’entreprise
qui s’industrialise et lui permet notamment d’augmenter ses capacités de volume
et facilite le rangement des profils aluminium en amont de la fabrication des brise-soleil
Mais tel n’a pas toujours été le cas. Car le marché historique de Tecauma qui se lance en 1977 a d’abord été celui de la brique et de la tuile où l’entreprise commence par proposer des solutions d’empilage, de convoyage et de manutention. Avant de mettre le pied dans les années 2000 dans le secteur de la fermeture qui représente désormais 60 % de son chiffre d’affaires. Aujourd’hui encore, la société qui comprend 75 collaborateurs est multisecteurs et continue d’officier dans les matériaux de construction, mais aussi dans le domaine de la métallurgie avec notamment son Robotflex, un robot polyarticulé qui permet d’alimenter des centres d’usinage ou des fraiseuses à commande numérique. Avantage de ce portefeuille multicartes : les passerelles technologiques entre les trois secteurs d’activité. « Nous avons commencé modestement il y a vingt ans dans le secteur de la menuiserie industrielle en proposant des convoyeurs car nous étions géographiquement proches de gros acteurs du marché, tels que K•Line ou Lapeyre », résume Gervais Gendre, ingénieur technico-commercial et chef de marché menuiserie chez Tecauma. « Nous avons très vite étoffé notre gamme de solutions en proposant notamment des cadreuses-visseuses automatisées. Sur les trois marchés sur lesquels nous sommes installés, les dispositifs de stockage et de convoyage se ressemblent, avec toutefois des spécifications particulières propres à chaque activité en termes notamment de charges et de cadences ».
© Tecauma
Les solutions de stockage vertical de Tecauma sont une alternative plus abordable
aux dispositifs plus complexes tels que les transstockeurs
Des transstockeurs toujours plus hauts
Il faut dire que Tecauma possède une organisation qui lui permet de maîtriser la chaîne complète de ses solutions qui comprend également le montage avec ses propres équipes. Un bureau d’études mécanique, un bureau d’études automatisme, des informaticiens, des roboticiens : tout est pensé en interne de A à Z. Une prise en main essentielle pour coller à la demande du client. C’est d’ailleurs un client particulier qui a fait bouger les lignes chez l’industriel vendéen : l’entreprise Janneau. En 2007, cette dernière formule une demande à Tecauma : elle a besoin de s’équiper d’un transstockeur mais aucun fabricant français ne fournit ce type de matériel. Tecauma se met alors à la tâche et lui livre son premier transstockeur qui sera le premier jalon pour le lancement d’une gamme à part entière baptisée Tec’Up et qui reste aujourd’hui encore la fierté de l’entreprise. D’autant que conçu d’abord pour la menuiserie industrielle et le stockage des profilés aluminium, le Tec’Up trouvera très vite preneur dans le secteur de la métallurgie pour le stockage des produits acier. Aujourd’hui, Janneau possède trois de ces machines, tandis qu’une trentaine sont actuellement en activité dans l’Hexagone. Et depuis 2007, la solution a su évoluer. En effet, si le Tec’Up H8 se limitait à une hauteur de bâtiment de 8 m, les versionssuivantes ont vite permis d’atteindre 12 m. Ce produit possède une interface informatique évolutive qui permet d’entrer directement en communication avec l’ERP du client », détaille Gervais Gendre. « Nous avons pensé le Tec’Up spécifiquement pour les menuisiers qui fabriquent des fenêtres pour notamment le stockage de produits longs, mais aussi le stockage à plat des ouvrants. Nous sommes par ailleurs en train de travailler sur un nouveau transstockeur qui répond à une commande et qui par la suite sera intégré à notre gamme ».
La force de Tecauma s’appuie sur une base très standard avec une adaptation très personnalisée en fonction des impératifs industriels. Les zones de chargement et de prélèvement sont ainsi calées sur les nouveaux process, et notamment sur un besoin de stockage plus haut pour des produits plus longs. Mais aussi plus nombreux. Avec la multiplication du nombre de références, il a aussi fallu s’adapter. « Quelques années en arrière, les clients avaient du mal à comprendre le retour sur investissement d’un transstockeur, mais celui-ci s'est peu à peu imposé comme un outil indispensable, car stocker mieux veut dire stocker moins », poursuit Gervais Gendre. « A ce premier avantage de gestion optimisée du stock s’est ajoutée la diminution des manipulations car ce n’est plus l’opérateur qui cherche les références, mais les références qui viennent à l’opérateur. Dans une période où la main d’oeuvre qualifiée fait cruellement défaut, ce type de dispositif permet aussi de travailler avec moins de personnel tout en garantissant le bon approvisionnement des centres d’usinage ».
Un avantage notoire bien compris par l’entreprise Fybolia qui s’est récemment équipée de deux transstockeurs Tecauma. Une tendance de fond car désormais, ce type de solution de stockage automatisé ne concerne plus seulement les gros faiseurs. Par ailleurs, Tecauma qui joue la carte du Made in France, reste à ce jour le seul fabricant hexagonal de transstockeurs. Mais le vendéen est loin d’avoir tout misé sur un seul produit. Il propose également du stockage de produits lourds avant et après usinage avec des solutions par luge et par casier, avec aussi du stockage à l’horizontal de cadres assemblés. La tour de stockage s’apparente quant à elle à un transstockeur, à la différence que sa capacité de stockage vertical est bien moindre.
© TIV (Groupe Devglass)
Chez TIV, une installation Hegla unique au monde accueille, coupe, alimente sur deux niveaux deux lignes d’assemblage de vitrages isolants
via un tri dynamique en un flux continu 4.0 capable d'assumer jusqu’à 3 coupes en simultané de panneaux de 2,50 x 4,50 m ;
elle regroupe le magasin de stockage du verre "Remaster", le pont de coupe "RapidLam", le retourneur l’ascenseur et le convoyeur :
à l’arrivée, productivité, sécurité et qualité exceptionnelles alignées dans la philosophie du groupe, "Tout en ligne et ne plus toucher le verre".
Sur un étage, la Streamlam réduit de 50 % l'occupation au sol et permet ici d'économiser 1 000 m² supplémentaires de surface
Le magasin en tour Kasto Unitower s’installe chez Werner Weitner
© KASTO Maschinenbau Afin de rendre ses processus de production et de logistique
Afin de rendre ses processus de production et de logistique plus efficaces, le spécialiste bavarois de l'ingénierie mécanique Werner Weitner a décidé de centraliser une grande partie de sa production dans un hall nouvellement construit sur le site de son siège social à Eichstätt, en Haute-Bavière. Avec deux systèmes de magasin en tour de type Unitower, le groupe allemand Kasto a apporté une solution ergonomique et économique permettant un gain de temps et d'espace. Son parc machines dispersé dans plusieurs bâtiments a ainsi été regroupé au sein d’un même ouvrage spécialement construit. L'entreprise de construction mécanique fabrique principalement des aciers et divers alliages, mais aussi de l'aluminium et des matières plastiques. Le portefeuille va des prototypes à la production à grande échelle. Cette grande variété de matériaux nécessite des capacités de stockage conséquentes. Dans le passé, Werner Weitner utilisait différentes zones de stockage manuelles pour conserver les matières premières, ce qui rendait la manipulation extrêmement inefficace. L'entrée ou la sortie ainsi que le transport vers les différentes machines de traitement prenaient beaucoup de temps et de main d'oeuvre. Au cours de la construction du nouveau hall, la technique de stockage devait donc également être automatisée. Cette décision s'est inscrite dans le cadre du projet interne "Weitner 4.0", dont l'objectif visait à optimiser durablement tous les processus de l'entreprise. Le choix s’est porté vers des solutions Kasto avec l'installation de deux systèmes de magasin en tour de type Unitower, la version 1.0 servant à contenir des pièces longues de jusqu'à 3 m, tandis que la version 2.0 est dédiée à des pièces allant jusqu'à 6 m de longueur. Les deux sont des tours jumelles indépendantes. Avec respectivement 52 et 41 cassettes, les magasins offrent suffisamment d'espace
© KASTO Maschinenbau Un transstockeur fournit les cassettes nécessaires |
Le stockage s’intègre à la ligne de production
Il y a deux ans, épousant la tendance du moment, Ryko s’est ainsi lancé dans le stockage automatisé avec navettes avec Graf Synergy, son partenaire industriel en automates de soudage et centres d’usinage. Ryko travaille ainsi actuellement sur l’installation chez Millet d’un transstockeur avec navettes automatiques. Chez le fabricant de portes et fenêtres comme pour d’autres projets conséquents, Ryko a déployé la modélisation 3D pour créer une implantation type des installations à venir sur des bases informatiques. Cette solution en sus de la visualisation permet de déterminer les cadences de tous les mouvements en cours de production.
© Ryko
La collaboration Graf Synergy et Ryko a permis en 2012 d’être les précurseurs
d’une révolution dans le monde de la soudure de cadres PVC avec le système
de soudage sans ébavurage seamles welding associant aujourd’hui
un label appelé Vperfect technology ; 10 ans après, plus d’une centaine
de machines Graf Synergy ont été livrées et installées en France et en Allemagne
« Le stockage fait donc désormais de plus en plus partie de la ligne de production, et s’il n’augmente pas la productivité, il sécurise toutefois les applications et les opérateurs », résume Alexandre Giraud. « Le stockage est aussi pensé comme un outil de gestion d’autant que le problème d’absence de personnel qualifié s’est ajouté aux difficultés du secteur. Aujourd’hui, le stockage moderne permet de dispatcher les cadres au travers de logiciels. L’opérateur devient de plus en plus un gestionnaire de machines. Ce qui change désormais, c’est que le panel de solutions est si large que nous pouvons répondre à tous les types de clients, peu importe les moyens de stockage à mettre en œuvre. Des dispositifs simples peuvent solutionner des problèmes de stockage sans nécessairement engager de gros investissements. Les petits industriels peuvent ainsi s’équiper aisément de solutions de stockage qui à leur niveau leur permettent d’être aussi flexibles que celles des grands fabricants de menuiseries ».
Concepteur et fabricant d’équipements industriels et de postes de travail sur mesure, l’entreprise MZR située à Landevieille en Vendée est présente sur le marché depuis 2006. La société d’une trentaine de salariés s’adresse aussi bien à l’artisan avec un petit poste ergonomique qu’au gros faiseur avec des lignes de montage complètes.
© MZR
Le concepteur de solutions MZR propose de nombreuses
solutions de stockage notamment, le classique convoyeur à dosseret
Dans le domaine du stockage, les solutions sont également adaptées à la structure industrielle. Si la petite entreprise est davantage focalisée sur du chariot, du buffer ou du stockeur multiproduits manuel, le gros faiseur est davantage en demande de solutions de stockage pouvant être assistées mécaniquement, motorisées ou complètement automatisées.
Pour satisfaire tout le monde, MZR a ainsi mis au point des convoyeurs à dosserets, des navettes manuelles ou motorisées, des buffers multicases avec navettes mobiles ou encore des chariots. Le maître mot : des systèmes évolutifs. « Ce qui perturbe les flux et le stockage, ce sont les menuiseries hors formats comme par exemple les baies à galandage ou les baies coulissantes », précise Jean-Marc Boisson, technico-commercial chez MZR. « Il faut donc proposer des systèmes sur mesure en partant du principe que nous recherchons le minimum d’automatisation et le maximum de flexibilité dans l’atelier. Les industriels nous demandent d’avoir des flux et des stockages qui ne soient pas figés dans le temps, mais évolutifs. On revient un peu sur le tout automatisme avec des postes individuels très adaptatifs, avec des flux qui peuvent être motorisés mais aussi du simple convoyage à rouleaux par exemple. Cela répond à la demande de leurs propres clients qui peuvent avoir des menuiseries hors standards, alors que les systèmes tout automatique misent principalement sur des formats prédéfinis. C’est donc un mouvement à rebours de ce qui se fait pour les centres d’usinage où l’heure est au tout automatique ». Toutefois, le semi-automatique a le vent en poupe.
© MZR
MZR est présent depuis 2006 sur le marché de la transitique dédié au secteur de la menuiserie industrielle
Le propre domaine d’expertise de la menuiserie industrielle
Si l’intelligence se trouve encore du côté de l’opérateur, tous les mouvements comme les déplacements, les basculements, les mouvements de charge… sont de plus en plus assistés et motorisés. « Les produits deviennent de plus en plus lourds, et notre objectif est le zéro port de charge y compris sur des lignes complètes », poursuit Jean-Marc Boisson. « Nous avons ainsi réalisé des lignes full transitique notamment pour DC, totalement sans port de charge du début jusqu’à la fin. L’optimisation des flux et du stockage passe nécessairement par la fin du port de charge car on gagne en sécurité mais aussi sur les temps masqués, c'est-à-dire sur les opérations que l’opérateur n’est pas censé faire. L’essentiel, c’est de concentrer précisément les opérateurs sur leur tâche afin qu’ils ne soient pas perturbés par tout ce qui est lié au transport, au stockage et à la manutention ».
Si MZR étudie tous les postes en pensant flux entrants et flux sortants, le concepteur doit également prendre en compte de plus en plus la nécessité d’intégrer une ligne pour les réparations, le recyclage ou encore le traitement conformité. « On nous demande d’intégrer des moyens de stockage et de transitique pour des pièces qui peuvent sortir de la ligne, pour du recyclage, de la réparation, et de la réintégration dans la ligne », note Jean-Marc Boisson. « Cela fait partie de la productivité globale des lignes et cela rentre de plus en plus en compte dans la conception et la demande des clients. La menuiserie industrielle a su créer son propre domaine d’expertise avec des équipements adaptatifs et réalisés sur mesure ».
© MZR
Le chariot motorisé omnidirectionnel radiocommandé Omni’Lev de MZR
permet le déplacement de charges lourdes de grandes dimensions
© K•Line