Optimisation de l’espace en atelier : aménagement et compacité au rendez-vous
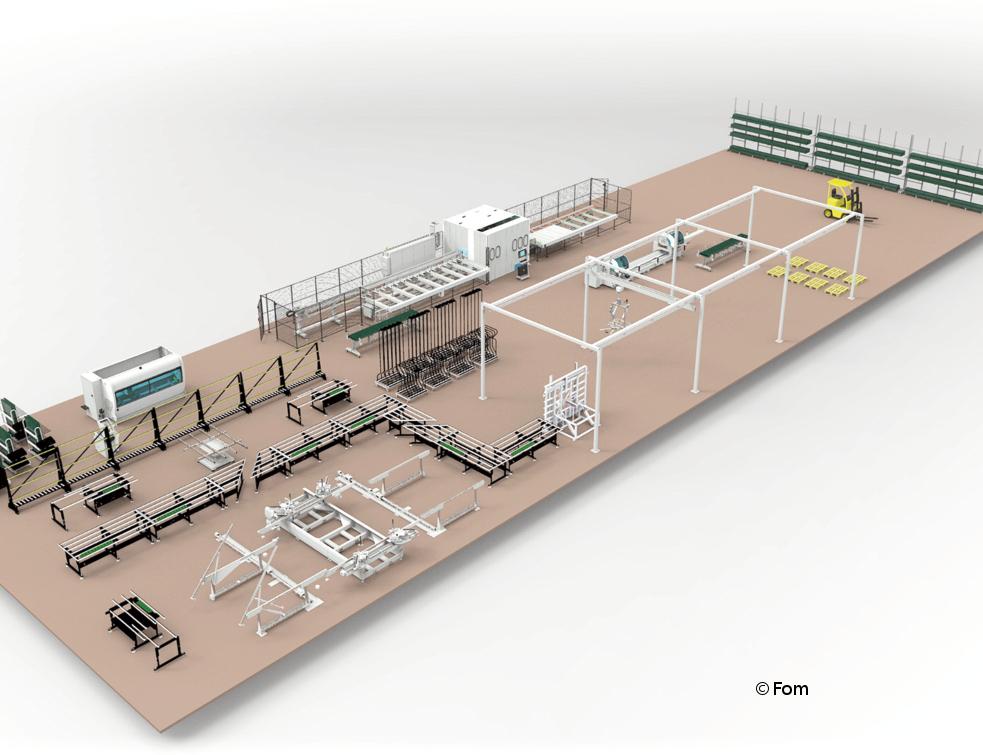
Véritable problématique, l’optimisation de l’espace en atelier concerne tant les industriels que les fabricants de machines-outils. Mais des solutions existent.
L'optimisation de l’espace en atelier est une préoccupation des clients et des industriels français ou européens », constate Pascal Royannais, directeur commercial de l’activité verre chez Intermac. « On s’aperçoit même qu’elle devient une priorité chez les clients confrontés aux contraintes d’agrandissement et au réaménagement de leurs ateliers ». Pas simple, en effet, d’agrandir les bâtiments existants, par exemple, en région parisienne. Pour sa part, Jean-Christophe Colombo, gérant de la société éponyme, souligne : « compte tenu du prix du m² à Paris, en région parisienne ou à Marseille, la place est un souci très important pour nos clients, les petits comme les grands ».
Bottero : les stocks au secours de l’espace
|
Pour Alexandre Giraud, responsable commercial chez Ryko France, « c’est un sujet qui tient à coeur les professionnels », remarque-t-il. « Même si c’est un peu moins vrai aujourd’hui, car les nouvelles usines sont suffisamment grandes, tout le monde cherche à gagner de la place ».
Un sentiment partagé par Christophe Garde, directeur associé chez DGM et Gilles Vignolles, chargé d’affaires chez 3M - Maison Machine pour Menuiserie. Le premier indique « que l’on cherche à optimiser l’espace avant d’agrandir les locaux », le second « qu’il s’agit, selon les lieux, d’une vraie préoccupation car les terrains sont rares et les bâtiments onéreux. Clairement, c’est une donnée qui entre dans le cahier des charges ».
Solutions astucieuses
Gagner de la place en atelier passe par deux solutions principales. Tout d’abord, le réaménagement de l’espace. Une préoccupation telle, que les professionnels de la machine-outil aident leurs clients dans cette tâche. « On nous demande comment aménager l’atelier pour positionner la machine », indique Gilles Le Bagousse, responsable commercial chez Fom France.
Afin de répondre à ces demandes, l’entreprise propose, depuis 3-4 ans, un service de logiciel 3D. D’ailleurs, lors du prochain Batimat, Fom présentera CARL (Custom Augmented Reality Layout), une application nomade conçue pour être utilisée sur tablette tactile ou PC chez le client par les représentants. « Il s’agit de suivre le flux de fabrication en partant des livraisons jusqu’aux expéditions », ajoute Gilles Le Bagousse. « D’amener les éléments d’un point A à un point B sans complication, ni poste entonnoir bloquant ce flux. On aménage l’implantation sur un plan, on la visualise et la peaufine avec le client ».
Christophe Garde précise, « nous conseillons nos clients sur la réimplantation générale au travers de l’optimisation des flux et menons des études d’implantation. Le m2 est cher et ils n’ont pas envie d’agrandir leurs locaux, surtout actuellement. Les navettes et stockeurs répondent à cette problématique, ainsi que les machines multifonctions ».
Situation identique chez Colombo. « Nous donnons souvent des conseils sur l’implantation de l’atelier », explique Jean-Christophe Colombo. « Par exemple, pour l’aluminium, il est judicieux de placer les postes, débit, usinage, assemblage, en face à face. Quant aux machines qui ne servent pas tous les jours, il est intéressant de les placer sur roulettes ou palettes pour les déplacer aisément lorsque l’on en a besoin. L’essentiel est de s’inscrire dans le flux de production, de prendre son temps pour situer, avec justesse, les postes de travail. Sinon, on risque de multiplier les problèmes ».
Implantation et gain de place pour la Combi de JC Colombo avec le stockage des tôles en hauteur et le rack dédié aux chutes sur le côté. L’opérateur a donc une cisaille et une plieuse, plus son stock dans un espace de 5 x 3 m © JC Colombo
Pour sa part, Armand Nagel, gérant de Nagel, remarque que « de nombreux chariots mobilisent de la place à proximité des postes de travail. Il faut organiser les flux et créer des postes de travail extensibles et réductibles à la dimension dont on a besoin grâce à des bras et plateformes télescopiques. Réduire la surface utile de travail et, si possible, spécialiser les postes de travail pour éviter de multiplier les outils, accessoires, etc ».
Quant à Daniel Kolopp, gérant d’Hegla France, il indique : « dans le verre, le nombre de références a explosé puisque l’on est passé de 15 à 100 en 25 ans. Outre les différents stockages (mobiles, manuels, motorisés, automatiques), l’approvisionnement des machines a évolué. De feuille par feuille et manuellement au début, il s’effectue, maintenant, automatiquement et par paquet pour les produits à forte rotations ».
Approvisionnement des lignes de production à partir du système de stockage compact Hegla © Hegla
Autre solution : miser sur la hauteur. Une possibilité encore peu mise en oeuvre. « Nous avions lancé des machines travaillant verticalement dans les années 90 avant de revenir aux solutions classiques pour des raisons économiques », rappelle Alexandre Giraud. « A cette époque aussi, les bâtiments industriels étaient moins chers. Par conséquent, il était plus cohérent d’agrandir les locaux ». Mais les temps changent. « Chez Mecan’Outil, on y travaille déjà », se réjouit Emmanuelle Albrecht, directrice générale. « Il est possible de développer des projets utilisant des robots avec des outils positionnés à la verticale. D’ailleurs, nous l’avons déjà fait ».
Corelec mise sur les profilés laqués
« La solution est simple », explique Lionel Fraysse, responsable technique laquage chez Corelec. « Il suffit d’enlever le stock de barres et de le remplacer par une machine à laquer ». Une boutade plus sérieuse qu’il n’y paraît puisqu’un stock de profilés coupés à longueur et prêts à être laqués est moins gourmand en place qu’un stock de profilés bruts. « D’ailleurs, nombreux sont les menuisiers aluminium à l’avoir fait », précise Lionel Fraysse. Car les avantages sont nombreux : réduction des stocks et des chariots et/ou stockages tampon ; flux très court pour la mise en couleur rapide de dépannage et de petites séries ; réponse client réduite (passage de 3 semaines de délais à 1 semaine) ; réduction des chutes ; suppression des encours ; réduction des queues de chantier ; suppression de l’interface de contrôle et de gestion logistique de la sous-traitance laquage.
Dans cette réalisation de Corelec chez Lacroix Portes Automatiques, la place de la machine de laquage a été gagnée sur le stock de barres laquées et les chariots de débit, de laquage en attente de sous-traitance extérieure, de montage ou de contrôle en retour de sous-traitance © Corelec |
Chez DGM, on raisonne en 3D pour l’implantation dans les nouvelles usines. Car le constat est sans appel : une dizaine de mètres reste inutilisée en hauteur. « Nous disposons de belles hauteurs dans les bâtiments récents », confirme Christophe Garde. « Il est possible d’y stocker les cadres via des tours de stockage à emprise réduite au sol. On construit aussi des mezzanines avec plateau pour les machines-outils ». Des solutions qui commencent à entrer dans les moeurs.
La tour de stockage de cadres ouvrants bois/aluminium/PVC de DGM Industries a une capacité de 24 cadres. Son empreinte au sol est très limitée puisqu’elle profite de la hauteur des usines © DGM Industries
Des machines compactes
Seconde possibilité, les machines multifonctions et/ou compactes mises au point par les industriels pour répondre aux contraintes de leurs clients. « Même si les fabricants essaient de réduire les volumes des machines, ce n’est pas possible pour tout le monde », avertit Alexandre Giraud.
Pour sa part, Intermac a mis au point la table Genius LMAC 61 qui permet de gagner 2 300 à 2 500 mm sur la longueur totale de la ligne, et même un module, puisqu’il n’y a pas de table intermédiaire. « Il est aussi possible de positionner la table dans l’autre sens », explique Pascal Royannais. « En effet, le pont de coupe est, normalement, fixé sur la largeur. Pour optimiser certains ateliers, Genius RSA a un pont de coupe sur la longueur ».
Même chose pour le centre d’usinage Vermax (il peut aussi se placer contre un mur) sur lequel le verre est en position verticale. Résultat : une emprise plus faible au sol. Pour Gilles Le Bagousse, « les machines sont plus longues mais elles condensent la place car elles limitent les opérations de reprise. Néanmoins, il faut toujours tenir compte de la longueur des profilés et du stockage ». Pour Emmanuelle Albrecht, « face à cette préoccupation de plus en plus prégnante, on raisonne place quand on conçoit une machine. Ce n’était pas forcément le cas auparavant. Aujourd’hui, on essaie de gagner de la place en longueur et en largeur ».
C’est en cela que les machines multifonctions gagnent du terrain. « Même si elle est imposante, une machine qui assure quatre ou cinq fonctions, sans chariot, ni stock intermédiaire, nécessite une moindre surface au sol », indique Christophe Garde.
Pour sa part, Gilles Vignolles considère qu’il existe deux façons de gagner de la place. Primo : réduire les encours de production. « Les fabricants font en sorte d’être opérationnels et efficaces sur le changement d’outils », précise-t-il. « Ainsi, avec les machines du groupe allemand Weining, on est passé de 45 à 10 min ». Secundo, regrouper les opérations. « Auparavant, on morcelait les opérations, avec 3 à 6 machines et des stocks tampons entre chacune », complète Gilles Vignolles. « Aujourd’hui, elles sont regroupées sur une seule machine. Au début, les choses sont un peu difficiles à mettre en place. Il s’agit, en effet, d’un changement de culture et d’une nouvelle manière de travailler ».
Les industriels innovent
Dans cette quête de place, les fabricants de machine-outils mettent la main à la pâte. Ainsi Intermac va plus loin et apporte un service commercial complet à ses clients avec Jean-Louis Piscina, responsable de l’activité industrielle. « Cet ancien industriel de la miroiterie apporte ses compétences, son expérience, sa vision d’expert pour la réimplantation de l’atelier, le flux du verre et la gestion de ce flux », précise Pascal Royannais.
Comall propose des tables de montage extensibles, qui se déploient et se règlent selon les dimensions des menuiseries à monter. Mensurations : 2 100 x 1 400 mm fermée, 3 100 x 2 100 ouverte (ici le modèle JOB 15 – 2000) © Comall
De son côté, Ryko met en oeuvre pour le PVC, de nouvelles techniques de soudage qui supprime l’ébavurage. « On réduit ainsi l’espace de production de 60 % », précise Alexandre Giraud. « La nouvelle soudeuse SL4 FF n'a plus besoin de la table de refroidissement, les cadres sortent finis et ne nécessitent pas d’ébavureuse, ni de table de retournement. Les lignes de soudage conventionnel occupent des espaces allant d'un minimum de 85 jusqu'à 120 m2 et, dans certains cas, même au-delà. La nouvelle machine de soudage 4 têtes occupe seulement 25 m2 ».
Compacité aussi chez Fom Industrie avec la ligne de coupe et usinage avec lame 650 mm LMT 65. « Complètement automatisée, elle produit des pièces particulières, usinées et coupées sur mesure, grâce à un centre d’usinage multibroches et à une tronçonneuse avec sortie frontale de la lame », explique Gilles Le Bagousse. Pour sa part, Mecan’Outil a développé deux machines, une déligneuse de seuils qui tient sur 1 m2 et la poinçonneuse automatique à plateau rotatif PNC 15. Et Nagel distribue la table MKS de Ruchser GmbH avec convoyeur retourneur. Ce poste d’assemblagemontage, mis au point pour les menuiseries bois, PVC et aluminium est basculant, extensible, mobile sur rails et permet, en combinaison avec un convoyeur RU-RGAF ou RGAT, à un opérateur de manipuler seul une menuiserie 1 000 x 1 000 mm jusqu’à 3 000 x 2 800 mm pesant jusqu’à 250 kg.
M.L.