En verre et contre tout
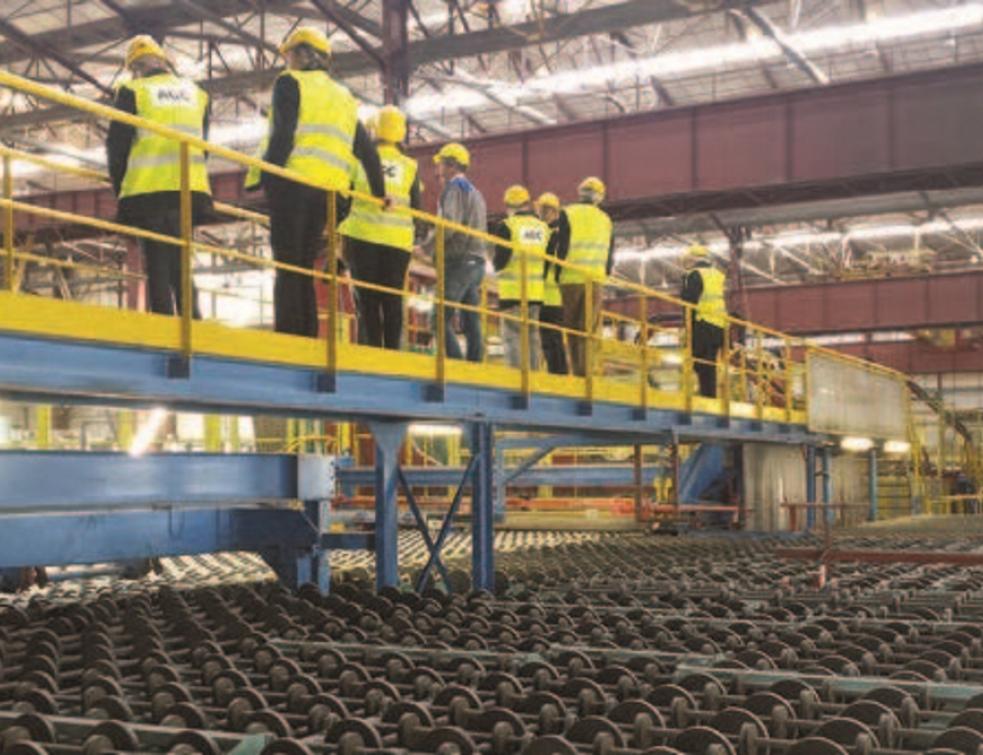
Pour célébrer à sa manière l’année internationale du verre, AGC Glass France a exceptionnellement ouvert les portes de son usine de Boussois dans les Hauts-de-France.
Une fois n’est pas coutume, le spécialiste du verre plat a convié fin mars un large panel d’ingénieurs de bureaux d’études à venir découvrir les coulisses de la fabrication des produits verriers qu’ils ont généralement l’habitude de prescrire pour leurs projets. Une occasion rêvée pour une soixantaine de professionnels aguerris de découvrir et comprendre le process industriel qui se cache derrière la haute technicité des produits verriers. Mais aussi une opération séduction pour la filiale française de la multinationale AGC qui n’a pas pour habitude de livrer sur la place publique ses secrets industriels. Les happy few triés sur le volet ont pu ainsi pousser la porte du site de Boussois situé près de Valenciennes, et faire un bond dans le passé d’un complexe industriel implanté dans cette petite ville du Nord en 1898. Véritable ville dans la ville, puisque l’usine d’AGC France se déploie sur pas moins de 57 hectares dont 13 hectares de bâtiments, avec deux lignes de float, Boussois produit actuellement 400 000 T de verre clair et extra-clair. Un volume divisé par deux depuis 2020 et les débuts de la crise sanitaire en raison de l’arrêt d’une des lignes. Mais un volume qui reste toutefois considérable. Du reste, le site dispose d’une capacité de stockage de 47 000 T et s’est spécialisé dans la fabrication de deux produits phare de la gamme : le Planibel Clearlite, un verre transparent destiné aux marchés de la vitrerie et du vitrage isolant, et le Planibel Clearvision, un verre hautement transparent servant notamment à l’élaboration de verres à couches.
© VMA/S.C.
Déployée sur 57 hectares, l’usine de Boussois située dans
les Hauts-de-France appartient au groupe AGC depuis 1999
et compte 13 ha de bâtiments notamment pour le stockage du sable
Des verres pour l’avion Concorde
C’est ici à Boussois qu’ont notamment été fabriqués les cockpits des avions Concorde, mais aussi les vitrages qui parsèment les façades de l’Opéra de Sydney en Australie. Une petite fierté pour un site qui emploie 135 salariés et accueille également le siège social de l’entreprise. Si la ligne B1 est à l’arrêt en attendant une modernisation moins énergivore de ses outils de production, la ligne B2 est quant à elle logée dans un bâtiment long de 500 m qui engloutit chaque année pas moins de 300 000 T de sable extraits d’une carrière près de Soissons. Un sable qui mélangé à de la soude passe dans un four à aéro-combustion chauffé au gaz montant à 1 600 degrés. Il faudra déployer en sus chaque heure 5 MW de puissance électrique pour parvenir à créer du verre plat. Pour produire une tonne de verre, 3 MW d'énergie sont consommés par la chaîne de production. « Chaque quart d’heure, le four consomme l’équivalent annuel de la consommation en gaz d’une maison moyenne », compare Xavier Denis, directeur des opérations de l’usine de Boussois.
C’est ainsi 6 000 m³ de gaz par heure qui sont dévorés par la ligne B2, lesquels représentent 60 % du prix de revient du verre. Une quantité en phase avec le volume de verre qui sort des lignes : 700 T de verre sont fondues chaque année, soit 40 km de verre produits chaque jour. L’équivalent de 64 000 m² ! Si le verre reste un produit de haute technologie, sa fabrication reste pourtant étonnamment artisanale. Car les méthodes industrielles n’ont guère changé depuis le milieu du 19e siècle. Le secret : la température de refroidissement du verre. « La viscosité du verre change avec la température et la maîtrise de cette opération reste un métier artisanal », poursuit Xavier Denis. Le verre en fusion est porté à 1 600° afin de dégazer pour éviter de créer des bulles d’air dans le produit final, puis est refroidi progressivement. La coulée est ensuite répandue sur un bain d’étain afin de stopper son étalement. Sur une longueur de 170 m, ce bain va refroidir progressivement le verre grâce à des batteries de refroidissement pour le passer en sortie à 620°. Une température qui doit être respectée à la lettre, car en dessous de 610°, les feuilles de verre se brisent, entraînant un arrêt de la coulée. Le dernier incident de ce type a eu lieu en juin dernier et entraîné 15 jours de perte de production. En bout de chaîne, la température du verre a atteint 80°, une opération qui prend à peine 15 minutes. L’atelier de découpe, ultime étape de la production de panneaux verriers, permet à partir des chutes, de récupérer 20 % de calcin. Et de le réintroduire dans le process. Sur l’ensemble de son cycle de vie, cette opération de valorisation des déchets permet d’économiser 10 % de l'énergie nécessaire à sa production.
Consommer moins et plus propre
Parce qu’une demie tonne de CO2 est émise par tonne de verre produite, la question de l’impact environnemental est devenue centrale pour un verrier comme AGC. Si le secteur sidérurgique va bien au-delà de ce chiffre avec pas moins de 10 T de CO2 par tonne d’acier produite, l’industriel est toutefois bien obligé de balayer devant sa porte. D’autant que la hausse vertigineuse des prix de l'énergie et notamment du gaz, est en train de remettre au centre de l’échiquier la thématique de l’économie de la ressource. Pour ce faire, AGC va investir dans un outil de production plus vert. C’est tout l’enjeu de sa feuille de route environnementale présentée lors de cette visite. Avec des objectifs clairement affichés d’ici 2030 : une réduction de 30 % de ses émissions de gaz à effet de serre, une baisse de 20 % de sa consommation d'énergie et une réduction de 15 % de sa consommation d’eau.
Le verrier vise également la neutralité carbone à l’horizon 2050. Une ambition déjà en marche selon Laurent Delmotte, directeur du développement durable chez AGC Glass Europe. Et pour cause : depuis les années 90, l’industriel a déjà, par tonne de verre produite, réduit de 30 % ses émissions de CO2 pour son site de Boussois, en passant du fioul lourd au gaz. Vouloir atteindre en à peine dix ans ce qui a été fait en trois décennies place donc la barre très haute. Mais AGC veut se donner les moyens de ses ambitions. Le verrier compte ainsi remplacer le méthane par l’électricité ou l’hydrogène pour la fusion des matières premières. Sur ce point, la France a un avantage : en raison du nucléaire, l'énergie électrique est à la fois la plus décarbonée d’Europe, mais aussi la moins chère. « En France, moins de 100 kg de CO2 sont émis par MW, contre trois en Allemagne », rappelle Laurent Delmotte. « Le ratio entre le prix de l’électricité et celui du gaz pour fondre le verre va être une donnée centrale dans les mois et années à venir ». Un avantage compétitif certain pour le site de Boussois.
© VMA/S.C
Le four de la ligne de float B2 consomme à lui seul 6 000 m³ de gaz par heure
Parallèlement à cette recherche d’une source d'énergie moins polluante, AGC va augmenter l’apport de calcin avec la mise en place de circuits de recyclage des anciennes menuiseries. Le fabricant de verre va également diversifier ses apports de matières premières, mais aussi développer des solutions de captation de carbone avec une réutilisation dans le circuit de production. Mais AGC ne compte pas uniquement réduire ses émissions directes de CO2. Il veut aussi s’attaquer à ses émissions indirectes, lesquelles représentent un lourd tribut : la moitié de son CO2 émis, soit 1,8 million de tonnes sur un global de 3,9 millions de tonnes émises chaque année.
Un million de tonnes de verres recyclés par an
Pour y parvenir, AGC va augmenter la production et l’utilisation d'énergie renouvelable avec la mise en oeuvre sur ses unités industrielles de nouveaux panneaux photovoltaïques. Une réalité déjà sur le terrain depuis 2009 et qui a permis en 2020 d'autoproduire 25 577 MWh. D’autre part, la première éolienne a été construite en 2020 sur le site de Seneffe en Belgique. L’industriel va également augmenter le transport par barge et par train. Sur ce point, des avancées ont d’ores et déjà été conquises avec le lancement dès 2009 d’une ligne ferroviaire entre la Belgique et l’Italie. Actuellement, 56 % des matières premières (principalement le sable) sont transportées par bateau, péniche ou train, ce qui représente l’équivalent de quelque 50 000 camions en moins chaque année sur les routes d’Europe. En 2020, plus de 40 000 T de produits verriers finis ont également été transportés par train et par camion, soit environ 2 000 camions en moins sur le réseau routier par an.
AGC compte également favoriser le développement de nouveaux produits présentant de meilleures performances environnementales tout au long de leur cycle de vie. C’est déjà le cas de son vitrage Fineo lancé en 2019. Appartenant à la dernière génération des verres isolants sous vide, il est produit sur le site belge de Lodelinsart et recyclable à 100 %. Désormais, AGC Glass Europe recycle près d’1 M de tonne de verre chaque année, soit 700 000 T d’émissions directes évitées. Depuis 2002, les émissions directes de CO2 des usines de fabrication de float d’AGC Glass Europe ont baissé d’environ 11 % par tonne de verre produite.
© VMA/S.C.