La logistique à l’heure de l’automatisation
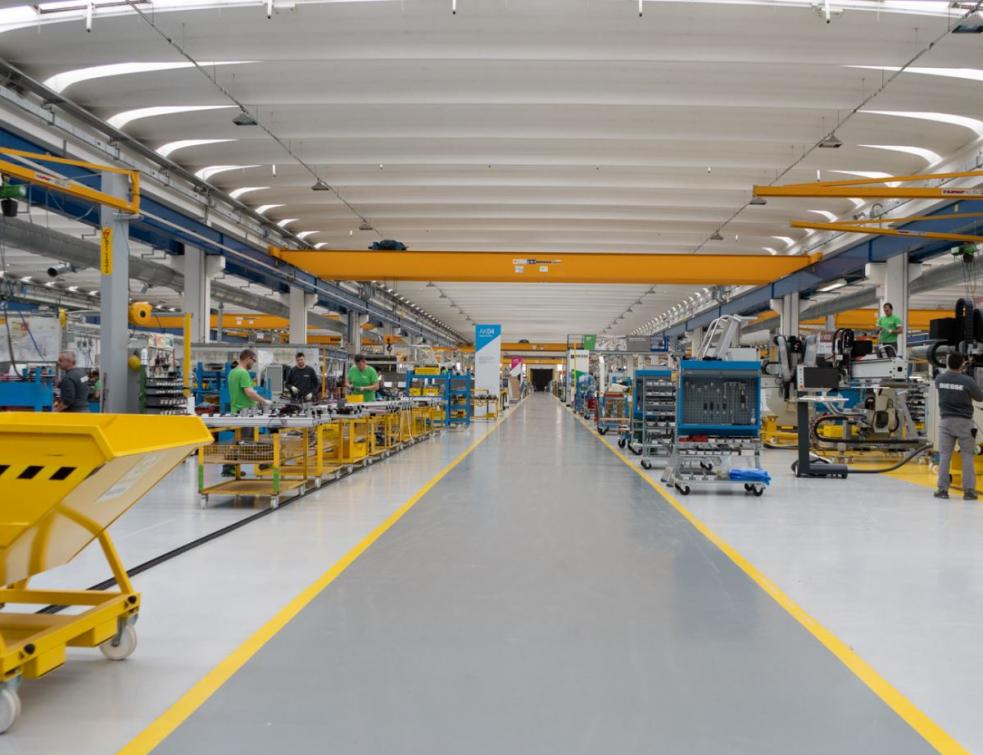
Le secteur de la menuiserie automatise progressivement ses lignes de production. Objectif : améliorer la logistique des flux, gagner en cadence et faciliter les conditions de travail des opérateurs.
« Ce sont des chiffres qui font, au propre comme au figuré, froid dans le dos : selon les derniers chiffres 2017 de la Sécurité sociale, les lombalgies représentent 20 % des accidents du travail, avec une durée moyenne d’arrêt de deux mois pour les personnes concernées »
Un chiffre en nette augmentation puisque ce pourcentage atteignait 13 % en 2005 . Véritable enjeu socio-économique et organisationnel, le mal de dos touche en priorité les salariés du BTP et a un coût non négligeable : 1 Md€ ponctionné chaque année dans les caisses de l'Assurance Maladie. Ce qui en fait, avec les Troubles Musculo Squelettiques (TMS ) et les pathologies liées à l 'amiante, le poste d’indemnisation le plus important. Un coût également pour les entreprises: 12,2 millions de journées de travail perdues en raison d’une lombalgie , soit 57 000 emplois à temps plein. Dans le secteur de la menuiserie, métier déjà fortement impacté par la raréfaction de la main d’œuvre, le mal du siècle est aussi devenu un véritable casse-tête. D’autant que face à un marché en plein rebond et dans un contexte de pénurie de matière première, garantir la cadence des lignes de production s’apparente à un véritable Rubix Cube.
© Bewap
Le bureau d’études Bewap travaille sur le développement de systèmes automatisés sur les postes
peinture permettant de réduire la pénibilité au travail des opérateurs sur des postes répétitifs
La transitique au cœur des préoccupations industrielles
La solution réside donc en partie sur une refonte de ce que l’on appelle désormais communément par néologisme la transitique, à savoir la logistique interne d’une entreprise ainsi que l'ensemble des opérations permettant le convoyage, le transfert et la manutention de matières, de produits et d'information. Véritable science de l’organisation du travail, elle touche aussi le monde de la menuiserie qui, même s’il demeure sur un profil d’entreprises encore très artisanales, ne peut plus tourner le dos aux moyens modernes de production. Le bureau d’études Bewap suit de près ces tendances du secteur.
Concepteur de machines, la société basée à Tarbes apporte son expertise pour intégrer ses installations dans les flux logistiques de ses clients. Son approche : proposer des systèmes d’aide à la manutention au niveau du placement des charges et de l’accrochage des pièces. Spécialiste à la fois de machines à laquer permettant la mise en peinture soit liquide, soit en poudre de menuiseries complètes, mais aussi de bancs d’essai, Bewap a fait de l’économie de matière le maître mot de ses interventions. Mais pas seulement. Car il s’agit également d’enlever aux opérateurs des gestes répétitifs qui peuvent à terme occasionner des problèmes physiques. L’intégration de la robotisation multiaxes d’éléments motorisés pour optimiser les flux notamment sur la partie consommables.
Les robots de peinture de la firme italienne CMA Robotics que Bewap intègre en complément de ses installations sont directement empruntés au secteur de l’industrie automobile, avec une adaptation de la programmation pour coller aux pièces, aux profils et aux cadres spécifiques au segment de la menuiserie. «Depuis quelques années, le coût des robots baisse fortement, ce qui permet de généraliser de plus en plus leur installation au sein des usines, principalement sur les postes peinture liquide où le geste se doit d’être le plus précis possible », explique Alain Marcusse, gérant de Bewap. « La manipulation d’un pistolet de peinture avec le poids au bout du bras est une position à risque car elle est répétitive. En robotisant certains postes, il est ainsi possible de libérer l’opérateur en supprimant un geste de peinture qui est une action de balayage toujours génératrice de tensions musculaires. Cela permet en définitive d’intégrer des outils qui vont remplacer le peintre, lequel sera davantage concentré sur de l’organisation en amont et sur le pilotage du robot, lequel peut travailler sur une plage de temps qui n’est plus contrainte.La régularité du travail s’en ressent immédiatement, tout comme la productivité » .
Fluidifier les lignes de production
Mais Bewap ne s’arrête pas à une automatisation de postes qui dans d’autres secteurs industriels ont depuis longtemps passé le cap de la libération de la main de l’homme. Dans le convoyage, la petite SARL pense également des outils d’aide pour faciliter le travail des peintres en installant par exemple des stations élévatrices qui vont permettre de descendre les pièces à hauteur d ’homme. Avantage induit : ces dispositifs bénéficient des aides des caisses d 'Assurance Retraite et de la Santé au Travail (Carsat).
Si sur les bancs d’essai, la problématique consiste à installer des flux d’air permettant aux opérateurs de ne pas être soumis à des renvois de peinture, reste l’évolution des produits eux-mêmes. Car les menuiseries, en raison de vitrages de plus en plus imposants, sont de plus en plus lourdes. Bewap réfléchit ainsi de manière continue avec des industriels partenaires à des solutions permettant d’intégrer aux bancs d’essai des ponts de levage ou des systèmes avec ventouses afin d’y amener de manière plus fluide les menuiseries, facilitant ainsi le travail des opérateurs tout en garantissant leur sécurité.
« L’outil de production suit indéniablement la tendance esthétique du moment avec des vitrages de plus en plus grands, mais aussi la tendance thermique de disposer de produits beaucoup plus isolants », poursuit Alain Marcusse. « La manipulation des menuiseries par un seul opérateur devient donc de plus en plus complexe, ce qui pousse à la mise en œuvre de système d’aide au port de charge. Pour cette raison, mes clients commencent à expérimenter l’exosquelette comme solution pour gérer la montée en poids de leurs produits. Les solutions qui existent sont aujourd’hui relativement accessibles financièrement et techniquement pour un industriel qui cherche non seulement à préserver son outil de travail, mais aussi les opérateurs qui sont dessus ».
© Groupe Biesse
La surveillance en continu des installations mises en oeuvre par le fabricant Biesse est pensée comme une aide primordiale au maintien de la productivité des menuiseries
Optimiser les chaînes de production passe désormais nécessairement par des machines équipées de solutions permettant de gérer la maintenance à distance. Cette option de logistique interne qui permet d’intervenir sur une installation sans avoir à déplacer d’opérateur est une tendance de fonds au sein du groupe Biesse.
Le groupe italien fort de 4 000 collaborateurs et d’un chiffre d’affaires de 560 M€ en 2020 se veut d’ailleurs un leader en matière d’usine 4.0. Il a ainsi développé en 2017 ce qu’il nomme doctement l’assistance cyber-physique en réalisant en collaboration avec l’entreprise de conseil Accenture une plateforme IoT baptisée Sophia, qui se veut le sésame pour simplifier et rationaliser la gestion du travail. Généralisée depuis 2018 à l’ensemble de ses machines, cette plateforme permet d’envoyer en temps réel des informations et des données pour optimiser les performances et la productivité des machines et des lignes. Les données relevées permettent de surveiller la production, d’analyser le fonctionnement des machines ou encore d’identifier les dysfonctionnements.
L’intelligence artificielle en embuscade
Objectif ultime : la compilation et la gestion de milliers de données terrain provenant du parc machines installé à travers le monde permet d’améliorer l’utilisation des équipements par les industriels.
« L’outil de pilotage de la machine intégrée est la garantie d’avoir toujours une solution qui permet d’éviter d’endommager l’outil de production », résume Arnaud Place, directeur service client de Biesse France. « Aujourd’hui, la priorité pour les industriels est de mettre en place un suivi des équipements pour optimiser le rendement. L’industrie 4.0 consiste donc à installer sur nos machines des programmes pour être sur du préventif, mais aussi du prédictif. L’intelligence artificielle proposée au travers de notre outil Sophia représente donc tout l’univers des services du groupe Biesse, qui passe aussi par l’amélioration de la chaîne de production ». Mais le fabricant italien de machines et technologie pour usiner le verre, la pierre et le métal sous la marque Intermac notamment, n’a pas attendu Sophia pour penser logistique. L’industriel propose ainsi depuis 2012 un logiciel de CAO dédié totalement autonome qui permet de faire de l’usinage 5 axes. Baptisé B_Solid, il possède l’avantage de ne pas fonctionner comme une interface, mais de piloter directement la machine en intégré. Avec un volume de 350 à 400 machines installées chaque année dans l’Hexagone, principalement chez des PME, la filiale française avec un CA de 50 M€ fait partie des wagons de tête du groupe Biesse dans le monde. Elle a de ce fait une vision aiguë des besoins des industriels de la menuiserie en matière de logistique interne. « Le marché français est fortement demandeur de nouvelles technologies, notamment en ce qui concerne le chargement automatique des machines », note Jean Luc Prunier, directeur du développement service chez Biesse France. « L’automatisation dont le but est d’enlever de la pénibilité en chargeant ou en déchargeant du matériel touche du reste des sociétés de plus en plus modestes en termes de masse salariale, et notamment des artisans de taille très modestes».
Un point de vue que ne renierait pas Daniel Kolopp, gérant de la filiale française du groupe Hegla. L’industriel allemand, spécialiste émérite de la conception et fabrication de machines pour la coupe, la manutention, le stockage et le transport du verre float et du verre feuilleté, a tout misé sur l’automatisation de ses systèmes. Il faut dire que le secteur s’y prête bien. « Les clients industriels que je rencontre me demandent tous d’automatiser pour être plus capacitifs et pour travailler avec de moins en moins de personnel, car il se fait de plus en plus rare », pointe Daniel Kolopp. « Les usines ont donc tendance à automatiser, souvent du lite loader jusqu’à l’entrée de la ligne de production. Nous sommes même capables désormais de faire fonctionner des lignes de coupe sans aucun opérateur, notamment pour de la découpe de verre feuilleté totalement autonome. Face à la pénurie de main d'œuvre, automatiser une usine apparaît la seule porte de sortie pour des industriels qui veulent continuer de produire ».
Limiter l’intervention humaine
© VMA
Les véhicules autoguidés - AGV (Automatic Guided Vehicles) Hegla se déplacent
en toute autonomie pour venir alimenter les lignes de production
C’est du reste grâce à l’automatisation que les activités commerciales d’Hegla se sont développées en France il y a de cela 26 ans. A l’époque, chez la plupart des menuisiers, la ligne de coupe consistait simplement en une table de rompage avec un chargement effectué à la main par l’opérateur. Hegla commence dès lors par approvisionner automatiquement les tables avec un dépileur, supprimant de facto toute intervention humaine avec des balancelles.
Seconde étape : la ligne de coupe elle-même avec la mise en place du rompage automatique en X, Y, et voire sur certains sites en Z. Il y a deux ans, Hegla s’est aussi lancé dans l’installation de systèmes de transport par véhicules autoguidés dits AGV (pour Automatic Guided Vehicles). Le chariot filoguidé qui a la particularité de pouvoir se déplacer de manière autonome pour alimenter les lignes de production, est venu remplacer le chariot à compartiments avec un stockage fixe. En raison d’éléments verriers de plus en plus lourds, son déplacement manuel était devenu de plus en plus problématique. Depuis une dizaine d’années, la perte de souplesse du chariot a donc poussé les industriels à chercher des solutions robotiques alternatives. « L’automatisation des sorties de lignes qui permettent de mettre les verres sans intervention manuelle sur des SortJets ou des chariots permet d’augmenter la productivité de 30 à 40 % », précise Daniel Kolopp. « Nous nous sommes en effet aperçus que la machine était capable de livrer beaucoup plus de verre que ce que l’opérateur était capable de descendre, non pas à cause de la vitesse mais du port de charge ».
Certains industriels ont donc également automatisé pour limiter la manutention, ce qui a pour effet direct la réduction des accidents de travail. L’équation est simple : supprimer le port de charge conduit à augmenter la productivité.
Sortir de l’artisanat pour entrer dans celui du flux
En limitant les manipulations, l’on augmente aussi la qualité des produits en réduisant considérablement les frottements synonymes de rayures et de défauts. « Dans le passé, les verriers qui produisaient 200 000 m² par an étaient considérés comme de gros faiseurs », précise Daniel Kolopp.
« Aujourd’hui, ceux qui ont automatisé leur outil de production, y compris la sortie des lignes, s’approchent des 500 000 m². Nous sommes donc sur des rendements exceptionnels, avec des usines françaises qui sont beaucoup plus productives que leurs concurrentes allemandes dans lesquelles le travail en trois postes est encore très peu courant. Cela est dû également à un mouvement de concentration du marché où trois gros acteurs se partagent 80 % de la production. La centaine d’entreprises qui se partagent le reste des 12 millions de m² qui sortent des lignes de production chaque année en France sont peu ou pas automatisées. A l’avenir, elles survivront en proposant des produits très spécifiques pour un marché de niche. Les autres fermeront leurs portes faute d’avoir manqué le coche de la conversion à la logistique moderne ».
Celles dont s’occupe Armand Nagel sont pour l’heure encore bien vivantes. Il faut dire que le PDG de la société allemande Nagel Maschinen- Vertriebs-und Konstruktions a de quoi les réveiller avec ses systèmes d’organisation des flux d’assemblage d’équipements de menuiseries pour organiser des cadences régulières.
Bureau d’études, distributeur en France des marques Ruchser, Pressta Eisele ou encore PBT pour les fabricants de menuiseries PVC, bois et aluminium, Nagel s’emploie depuis près de quarante ans à fournir des lignes de travail où les opérateurs sont capables de travailler seuls. « Sur les postes de travail, il faut définir des tâches bien précises, spécialiser les opérateurs pour optimiser leurs gestes et organiser les flux afin qu’en sortie l’on augmente la qualité et la capacité de production », détaille Armand Nagel. « Hormis pour le PVC où un grand pas a été accompli ces quinze dernières années, les menuiseries bois et aluminium, principalement des PME, continuent de travailler sur des tréteaux à l’horizontal, avec plusieurs opérateurs. Ces ateliers qui n’ont pas de cadence et où les flux sont très précaires cherchent donc des solutions pour améliorer les process ».
Le matériel de la marque Ruchser, un fabricant très versé dans l’amélioration ergonomique des postes de travail individuels, va donc permettre à l’opérateur de disposer d’une plateforme de montage réglable en largeur et en hauteur aux dimensions de la menuiserie.
© Ruscher
Le bureau d’études Nagel installe des machines principalement d‘origine allemande avec un leitmotiv :
un opérateur = une menuiserie
Individualiser le travail de l’opérateur
L’astuce est simple mais efficace : le poste de travail est basculant à l’horizontal à 180°, ce qui permet l’accès à la traverse supérieure sans effort physique inconsidéré. Une table mobile qui peut ensuite, en étant basculée à la verticale, être intégrée dans le convoyeur, permettant ainsi de pousser d’une seule main de lourdes menuiseries sur des dizaines de mètres. Épousant la philosophie d’un opérateur = une menuiserie, cette organisation permet non seulement d’économiser du personnel, mais aussi de le responsabiliser puisqu’il suit de bout en bout la fabrication de son produit.Loin d’être du travail à la chaîne, il s’agit au contraire pour les petites et moyennes commandes de permettre à l’opérateur de travailler individuellement pour atteindre une certaine cadence. Avec une cinquantaine d’installations en France, Nagel sent depuis une quinzaine d’année un regain d'intérêt des industriels pour ce type de solutions.
Une prise de conscience déjà acquise il y a plus de trois décennies en Allemagne et dans les pays scandinaves et qui commencent désormais à essaimer dans l’Hexagone, pays où le thème de la productivité du secteur industriel est récurrent. Si Ruchser propose des appareils mécaniques très simples pour soulager principalement les manipulations des opérations, le fabricant également allemand Lemuth va lui beaucoup plus loin : il propose des solutions identiques, mais en tout automatique.
Si Ruschser met à disposition de l’opérateur un poste où il bénéficiera d’assistances mécaniques mais où le travail à la main reste central, chez Lemuth, le cadre est retiré du convoyeur par un robot puis envoyé vers une installation de pose automatique des gâches, paummelles, tringles et autres parcloses.Pensé pour les grosses installations, ce système est adapté pour la production de 200 à 300 unités/ jour. Mais le développement de ces automates reste pour l’heure réservé aux menuiseries avec du vitrage collé, un produit qui demeure relativement rare et peu accepté en France contrairement aux pays de l’Est. Une solution technique qui a pourtant un avantage : la menuiserie gagne en rigidité et en robustesse dès lors que le vitrage participe au maintien du vantail. Mais le vitrage collé a justement cet avantage de permettre l’automatisation. Lemuth propose ainsi des lignes tout automatique qui permettent de produire près de 1000 menuiseries par jour, avec à peine deux opérateurs.
« Toutes les gammes de quincailleries ont été retravaillées et optimisées pour rentrer dans la fabrication automatique », explique Armand Nagel. « Cette réflexion initiée depuis les années 90 continue de s’opérer, mais avec des solutions désormais très abouties en termes de techniques d’assemblage et de montage ».
© VD-Industry
VD-Industry a fait du lean management un axe de travail pour optimiser la fabrication de ses menuiseries coupe-feu. La firme vosgienne a également fait le pari de réduire ses coûts de production en réduisant le gaspillage de la matière première
Le lean management en phase avec VD-Industry
Chez VD-Industry, spécialiste des menuiseries résistant au feu, c’est le lean management qui depuis quelques années déjà retient l’attention des dirigeants de l’entreprise vosgienne. Le lean management, ou l’art de produire en limitant le gaspillage, est une des tendances de fonds de l’évolution logistique des entreprises. Et le segment de la menuiserie n’y est pas étranger. VD-Industry s’y est donc penché avec d’autres concepts souvent inspirés des organisations japonaises, comme la méthode des 5S qui consiste à optimiser les conditions de travail. Basée sur le tri, le rangement, le recyclage afin de limiter les pertes de matériel et réduire les accidents de travail. « Depuis la création de la société, nous avons fait le pari d’une industrialisation des menuiseries vitrées résistant au feu qui en 2003 étaient faites uniquement de manière artisanale », explique Laura Ferry, directrice communication et marketing de VD-Industry. « Nous avons découvert le lean et nous avons été séduit par l’objectif de réduire nos coûts globaux d’entreprise en supprimant les gaspillages. Cela a notamment été une des raisons pour laquelle nous nous sommes lancés dans le challenge de l’ISO 9001. Tout a ainsi été retravaillé : surprocess, stock et transports inutiles avec l’intégration notamment de notre propre chaîne de thermolaquage, ou encore correctifs sur les erreurs avec une gestion de la qualité très pointilleuse. En parallèle et via notre logiciel métier, nous avons travaillé à l’optimisation des chutes de profilés afin de pouvoir les réutiliser pour d’autres affaires et ainsi réduire presque à néant le gaspillage de cette matière ».
© Portalp
La robotisation de certaines opérations répétitives et facteurs de stress physique est devenu le credo du fabricant Portalp
Fabricant de portes automatiques piétonnes, l’industriel Portalp est au fait de la problématique de manipulation des pièces lourdes : certains de ses caissons tout équipés peuvent atteindre 70 kg.
L’entreprise qui a inauguré en août 2020 sa toute nouvelle unité de production de 6 500 m² à Saint-Egrève dans la banlieue grenobloise, a ainsi mis en place un stockage dynamique de ses profilés sur les lignes de production.
Le transstockeur, outil de logistique massif
Ce nouveau système de transstockeur automatisé permet de prélever non plus des profilés mais des emplacements, qui forment des civières dans lesquelles sont disposés ces mêmes profilés qui sont mis à disposition de l’opérateur en fonction du plan de production.
À ce premier gros investissement qui a demandé à Portalp de dégager une enveloppe de plus d’ 1M€ s’est ajouté celui dans une ligne de débit automatique et d’un centre d’usinage 4 axes. Portalp a volontairement écarté l’idée de s'équiper en centre de débit usinage intégré et a préservé une scie manuelle en cas de panne sur le centre de débit afin de pouvoir travailler en mode dégradé. L’industriel dispose aujourd’hui d’une ligne automatisée qui identifie, coupe, et permet de gérer une trentaine de commandes dans la journée, soit entre 500 et 700 profilés différents. Ce centre d’usinage a principalement été motivé par le projet de développement du segment portes palières de quai qui nécessitent une intervention plus poussée que les portes automatiques piétonnes. Pour parvenir à des temps gamme par pièce de 45 min, le fabricant a également investi dans un système de manutention des vantaux qui permet grâce à un préhenseur de retourner les produits à 180°. « Travaillant en assemblage dit en joint portefeuille donc sans collage, nous sommes dans l’incapacité de faire de l’assemblage sur une ligne verticale, ce qui nous oblige à une pose à plat sur une table de vitrage pour la mettre à disposition sur nos systèmes de transport », résume Jean-Marc Guelton, directeur industriel de Portalp. « Le préhenseur à ventouses qui est une aide à la manipulation des verres et à la manutention des vantaux a également l’avantage d’être peu bruyant, très souple et facile d’entretien. Le but de l’ensemble de nos investissements productifs était de limiter le port de charges des opérateurs mais surtout d’augmenter notre volume de stockage en facilitant l’accessibilité des opérateurs aux profilés ».
Portalp a par ailleurs revu complémentairement le poste d’emballage des caissons en mettant en œuvre une table avec des cartons préencochés afin que les opérateurs ne se retrouvent pas en porte-à- faux lorsqu’ils déplacent les menuiseries. Résultat : sur ce poste mis en place en 2014, les accidents de travail dus à des lombalgies ont été divisésde moitié. Même chose pour le poste agrafage qui pouvait occasionner des TMS importantes et qui a été supprimé au profit du cerclage. Un petit chariot électrique permet en sus de soulager ce caisson en sortie de ligne de cerclage afin que l’opérateur puisse aller seul le déposer sur une palette prête à l’expédition. Portalp a également investi dans des postes de travail réglables en hauteur pour les ajuster en fonction des opérateurs pour qu’ils puissent faire de l’assis-debout en fonction des productions à faire. Des petites solutions techniques ajoutées à de plus conséquentes et qui ont fait porter la note totale à plus de 2 M€ pour l’industriel isérois. Le prix à payer pour entrer dans le monde de l’usine... à rêves.
photo ouverture © Biesse
Le groupe italien Biesse s’est fortement impliqué ces dernières années dans le développement de suites logicielles d’aide à la conception des produits et dans la conception d’équipements pour optimiser la productivité de ses clients industriels ; ses ateliers de production en Italie sont eux aussi concernés par la gestion logistique des flux
- -
Merci pour ces détails sur cette notion d'automatisation dans la logistique