Les Super Spacers® concrétisent le rêve " The Opus "
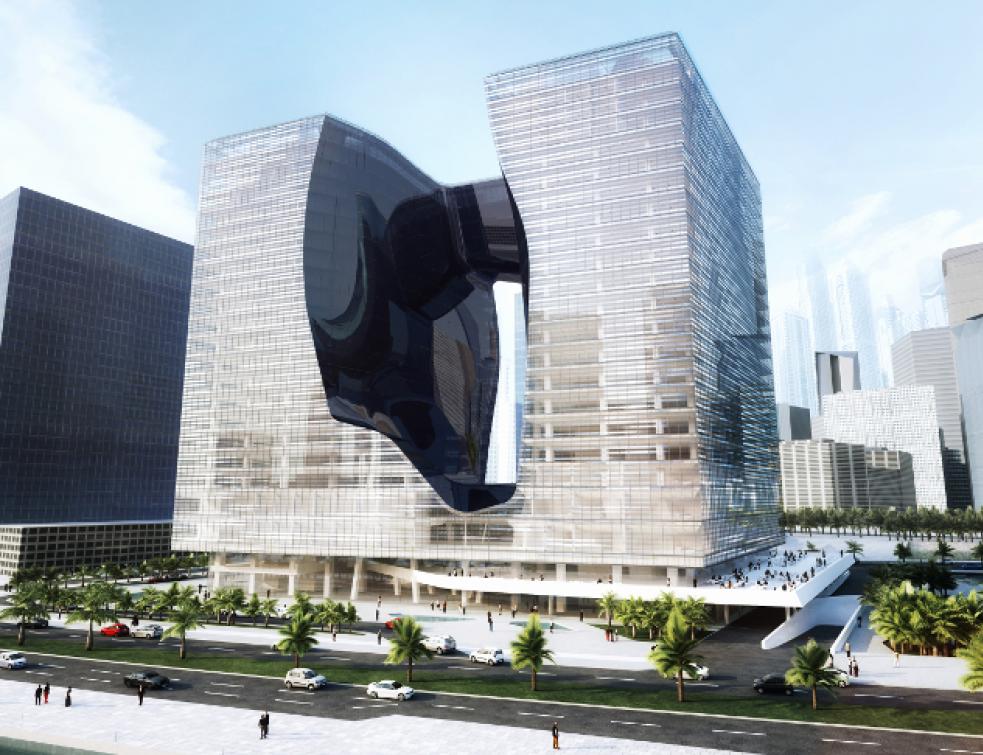
Pour le développeur de projet Omniyat, l'immeuble " The Opus " est " le bâtiment qui ne dort jamais ".
L'exceptionnel dynamisme de ses lignes architecturales repousse les limites du technologiquement faisable grâce à une conception avant-gardiste évidente au premier coup d'oeil. Situé dans le centre-ville de Dubaï, ce gigantesque puzzle en 3D intègre les Super Spacers® TriSealTM d'Edgetech.
La vision de Zaha Hadid : un cube flottant, évidé depuis l'intérieur
En 2013, faisant référence aux insipides bâtiments rectangulaires, Hadid déclarait au journal britannique The Guardian : " Nous ne bâtissons pas de jolis petits bâtiments. ". Pour les 21 étages de " The Opus ", implanté au coeur du quartier Burj de Dubaï, le plus formidable terrain de jeu pour architectes au monde, Zaha Hadid a imaginé un cube évidé depuis l'intérieur qui semblerait flotter au-dessus du sol.
Tel un glaçon qui fondrait sous le soleil du désert, " The Opus " offre aux personnes à l'intérieur un panorama exceptionnel sur l'époustouflante architecture environnante : le canal de Dubaï, le nouvel opéra ou la tour Burj Khalifa et le centre commercial de Dubaï. Débutée en 2012, la construction s'est achevée en octobre 2017 par les travaux sur l'enveloppe. Une fois l'intérieur décoré, l'immeuble accueillera un hôtel 5 étoiles, des restaurants, des bureaux et des appartements de standing.
" The Void " : un chef-d'oeuvre technique
Après que Zaha Hadid ait dévoilé en 2007 la spectaculaire conception de la " Dream Tower ", celle-ci a immédiatement attirée les plus grandes entreprises. Daniel Zhang, Responsable des ventes Edgetech / Quanex en Chine, explique la fascination qu'elle exerce sur les architectes et constructeurs de façade. " The Opus " était un saut dans l'inconnu. Au départ, personne ne savait comment la façade de verre organique imaginée par Hadid et couvrant quelques 6 000 m² pourrait apparaître dans son intégralité comme une surface fluide. En son état actuel, le bâtiment est un chef-d'oeuvre de technique à tous points de vue.
Chacun des 4 544 volumes verriers formant le vide bleu sombre est une pièce unique réalisée sur mesure. Ils sont, dans leur grande majorité, constitués d'un double vitrage isolant courbe. D'où l'impossibilité d'une installation automatisée de nos intercalaires. Nous ne pouvions pas non plus utiliser un espaceur rigide, n'épousant que difficilement les formes des vitrages et ne pouvant certainement pas être mis en oeuvre facilement.
Seul un intercalaire souple pouvait répondre aux exigences d'imperméabilisation et d'aspect. Sous un climat particulièrement chaud, un bord chaud doit posséder des performances exceptionnelles et les conserver des décennies afin de fermer hermétiquement l'espace entre les feuilles de verre. L'interaction thermique entre les zones chauffées par le soleil et celles à l'ombre génère en permanence de fortes contraintes mécaniques sur le composé du bord via le mouvement du vitrage.
Le jour, la façade reflète le ciel, le soleil, l'eau et l'architecture futuriste. La nuit, en revanche, " The Void " (le vide), illuminé par de spectaculaires installations de LED, connecte le bâtiment à sa vibrante métropole. Pour ce faire, chaque volume verrier a été pourvu de LED pouvant être individuellement commandées. Les façades transparentes des deux tours rectangulaires en béton armé sont constituées de doubles vitrages isolants traités anti-UV et d'imprimés points colorés de différentes tailles.
Tout en conférant à la façade une dynamique unique, ils reflètent la lumière et réduisent ainsi l'énergie solaire emmagasinée et l'éblouissement. Des équipes de différentes spécialités, comme celles du façadier Alu Nasa, des consultants de Koltay Façades à Dubaï, de Pilkington Glass, du fabricant de verre isolant Shennanyi, mais aussi du fabricant d'intercalaires Edgetech ont toutes apporté leur expertise dans la réalisation de " The Void ". Sa bordure inférieure se compose d'un toit en verre de forme libre qui couvre les niveaux de l'atrium.
Tout en haut du bâtiment, à 71 mètres d'élévation, les tours se rejoignent dans une passerelle parasismique, ondoyant élégamment sur 38 mètres ses plaques en double vitrage isolant et cadre aluminium montées sur une structure en acier. À elle seule, cette partie du bâtiment pèse 1 000 tonnes. Une modélisation 3D précise au millimètre pour les constructions primaires et secondaires en acier, les profilés courbes en aluminium, les éléments de fixation et les vitrages, a servi de base à tous les acteurs impliqués dans le projet. Plus de 10 000 profilés en aluminium cintrés individuellement ont été livrés du Danemark et des Pays-Bas, les vitrages proviennent de trois usines chinoises, et tout cela a finalement dû être assemblé précisément sur le site pour construire ce grand puzzle en 3D.
La quête de la vitre parfaite
Même le choix du verre a fait l'objet d'un long processus de sélection et de modélisation. Contrairement aux verres plans, il n'existe pas de données de résistance à la compression, à la traction et à la flexion pour les vitrages courbes. La courbure et l'épaisseur du verre affectant la rigidité à la flexion, les contraintes thermiques imposées par le soleil, l'absorption d'énergie maximale, le rayon de courbure minimal et les angles de courbure maximaux de chaque feuille de verre ont dû être calculés.
En outre, l'enveloppe de verre doit maintenir l'apport solaire sous une certaine limite afin d'éviter des niveaux de rayonnement reflété susceptibles de rompre sous la chaleur les façades vitrées en vis-à-vis. Finalement, il a été décidé d'installer un mélange de quelques volumes verriers plans et à courbure simple et de plaques de double vitrage isolant cintrés à chaud et à froid.
Le climat chaud qui prévaut à Dubaï impose au verre une charge thermique bien supérieure à celles des zones plus tempérées, et les vitrages sombres absorbent également davantage d'énergie. Le verre doit donc être aussi trempé que possible, un processus encore non testé au niveau industriel pour des vitrages isolants incurvés. Avec une trempe chimique, le verre cintré à chaud était trop cher.
La société Shennanyi a donc développé une technologie spéciale pour cintrer à chaud et tremper le verre. Elle comporte une chauffe du verre à 700°C, une trempe après le moulage et un refroidissement au moyen de buses à air comprimé pour augmenter la résistance à la rupture.
Ces plaques composées de 8 mm de verre à faible émissivité (enduit à l'intérieur), 16 mm de vide entre les vitrages, 6 mm de verre transparent, 1,52 mm de laminé coloré en PVB et encore 6 mm de verre transparent ont été fabriquées par Pilkington Chine. Afin de réduire les coûts, le nombre d'éléments cintrés à chaud a été minimisé et du verre isolant trempé et cintré à froid, plus économique à produire, a été utilisé à chaque fois qu'il était possible..
Laissez votre commentaire
Articles qui devraient vous intéresser
Dernière revue